In the color light addition method, equal proportions of the three color lights are added and mixed to form white light. Blue and green light are mixed into blue light; blue and red light are mixed red light; green and red light are mixed into yellow light and so on. These phenomena are unacceptable to most people, because people's broad practice is the subtractive method - the addition of color bodies, such as drawing color pictures, paint color matching, etc., are all subtractive principles, and for a For ink operators, it is not only necessary to understand the principle of color light addition, but more importantly, how to use the principle of subtractive color to guide actual operations. In the actual printing, according to the original design needs, sometimes need a special color as a foil. In addition, some products printed with four-color original inks are difficult to control due to overprinting problems and ink-to-ink balance. It is not easy to achieve an ideal reproduction effect. Sometimes, spot color printing is also required. Especially in packaging printing, some products pursue individuality. Therefore, More choices for spot color printing.
Carefully analyze the color draft or sample before deploying ink
When analysing a manuscript, it mainly analyzes the colors on the manuscript, the ink used, and the white ink. The basic principle is that the three primary colors of pigments are the basic colors of all inks, and they must remain the same. At the same time, it is necessary to make clear as far as possible whether the color draft is based on network printing or on-site printing. If the network printing is the main method, the ink color should be focused on the same color. If the printing is mainly based on the field, the ink can be mainly focused on the face color. If the two are combined, the background color when the ink is mixed. Both look and look.
When the color draft is analyzed, the color of the used ink should be analyzed. In general, the ink deployment operator is particularly sensitive to the observation of the ink color, and the components thereof can be seen, for example, the yellow ink, to be good at identifying it with yellow phase. The red phase still has a blue phase (or green phase). For a magenta ink, it must be good at discriminating whether it has a red phase or a blue phase (or a purple phase). For a blue ink, it must be good at identifying whether it has a red phase or With green phase (or with yellow phase). If green ink with a red ink with a red phase and yellow ink with a red phase are used, the resulting green color will be dark because it is actually equivalent to adding a magenta ink to the yellow ink and yellow ink (yellow + blue + product). Red = black), so observing the color of the ink is an essential basic skill for ink dispensing operators.
The basic principles of the deployment of spot color ink
Whether it is a dark or light spot color ink, the basic principles should be followed when deploying. This basic principle is based on the printing color and printing process. The main content includes the following ten points:
(1) Try to use the same type of ink and the same type of auxiliary materials. In addition, do not use three primary colors of inks that can be formulated with two primary color inks. Similarly, if you need a certain color to match, you must use the original color ink, so as not to reduce the brightness of the ink, affect the color and vividness. When deploying dark ink, the main color ink should be placed in the ink tray according to the weight of the ink, and then auxiliary colors and necessary auxiliary materials should be gradually added.
(2) Where the diluting agent is used as the primary color, or the primary color or the dark ink is used as the supplement, the formulated ink is collectively referred to as the light color ink. The method of light-colored ink is slightly different from the dark-colored ink in the method, and the dark ink is gradually added in the light-colored ink. Can not cut dark ink before adding light color ink, because the light color ink poor coloring, if you add dark ink in light-colored ink to adjust the alignment is not easy to adjust the hue, the ink will often make more adjustments.
(3) Prepare a small color sample before deploying spot color inks. This is to say that the color of the ink to be used is determined according to the initial hue of the original, and then a small amount of ink is weighed from the various colors of the ink using a balance, accurately weighed, placed on the ink adjustment table, and then the ink is fitted to the ink conditioner. Sample and original inspection, and make relevant records, keep it properly.
(4) When color mixing spot color inks are used, the complementary color theory is used to correct the color shift. For example, when the color of a certain complex ink is heavy, the yellow ink may be added to correct it; if the red color is heavy, the blue ink (such as peacock blue or sky blue ink) may be added to correct; if the black ink of the black ink is not enough, A slight amount of blue light is used as a color material, because the blue light is a blue ink with red light, which is beneficial to the blackness of the black ink.
(5) Grasp the hue characteristics of commonly used inks. In the actual operation, we must master the hue characteristics of commonly used inks. For example, in the deployment of light lake green ink, it is appropriate to use sky blue or peacock blue, avoid using dark blue to deploy, because the dark blue ink ribbon red, after joining, the color must be dark and not bright, the same reason, can not use reddish deep Yellow ink, and the use of partial yellowish yellow ink effect is better, and as an example, the deployment of orange ink when possible to use gold and red ink, because the gold red ink hue is red yellow, can increase the degree of ink vivid.
(6) Pay attention to the specific gravity of different inks. The proportion of ink is generally different, inks with similar proportions are easy to mix, and inks with a large difference in specific gravity can cause print defects, for example, green ink formulated with heavy lead-chrome yellow ink and peacock blue ink. For a long time, the small proportion of color inks will go up, and the larger ones will sink, so there is a "floating" flaw. If yellow ink made of organic pigments is used for deployment, rickets will disappear. In addition, due to the large white ink ratio, in addition to the requirements for cover and color matching when adding a small amount, try not to use white ink to dilute, in order to prevent poor color, fade and other quality problems.
(7) Mix white ink with color ink for spot coloring and white coloring for printing, and avoid the color difference due to the different white color.
(8) Make sure that the spot density is the same as the spot color ink. Generally, when the fresh ink just adjusted is close to the color of the print provided by the customer, the color change will occur after the new ink is dried, so the fresh ink that has just been adjusted cannot be lighter than the printed sample. That is the principle of "dark and shallow printing."
(9) Take into account the characteristics of post-press processing. When selecting the ink, the post-press processing conditions must be considered. If the print product requires a weld (such as a spray can), the fade-resisting ink should be selected on the edge of the weld. In the pre-printing preparation work, either the multicolor machine or the monochrome Machine, ink color deployment is a high-tech work. Iron printing ink is a kind of special ink. In order to meet the conditions of printing and high-temperature baking of metal printing, comprehensive consideration must be given to the choice of pigment and binder. If the operator does not understand the properties and color matching of the printing ink, the bright ink can not be mixed to achieve the desired appearance and quality.
Certificate |
ISO14001, ISO18000, ISO9001 Certificate,
and GS certificate from TUV Company of Germany.
|
Color | Various, according to your requirements |
Materials |
A. Plastic parts: Imported LLDPE E. Outer cover: Soft Covering PVC
(Different material is available according to your needs)
|
Advantage |
a.Anti-UV
b.Anti-static
c.Security
d.Environmental protection e.Uneasy to lose shape |
Function |
1.Can protect children safe when they playing indoor, and let they enjoy the play freely 2.Suitable for improving Children energy and imagination 3.Helping them grow up happily, cleverly, and healthily |
Age Range | Children |
Apply to | Amusement park, gymnasium, Kindergarten, Preschool, etc. |
Packing | Standard export packing |
Remark |
We can design and produce as your requirements |
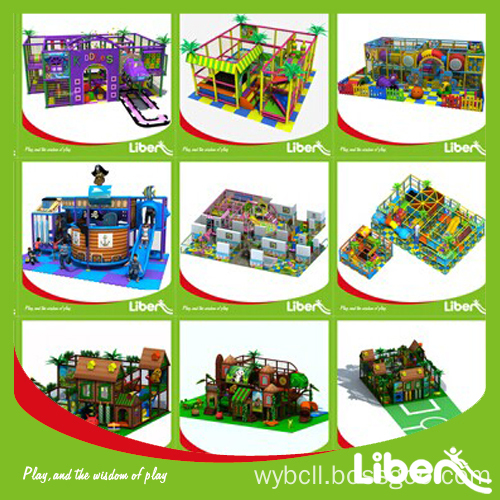
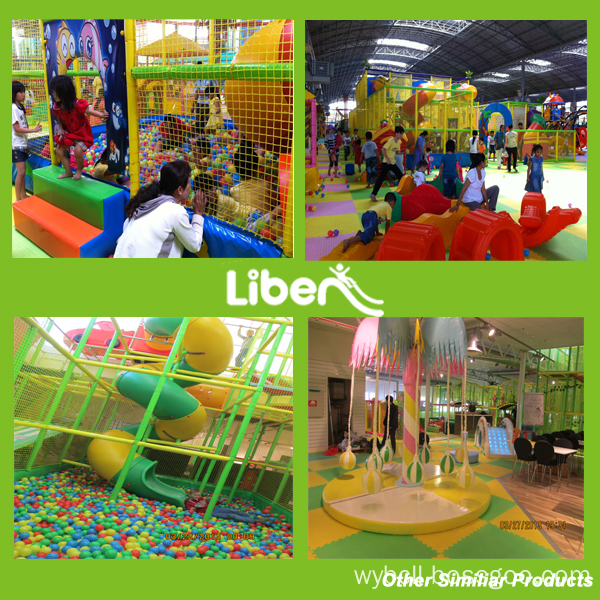
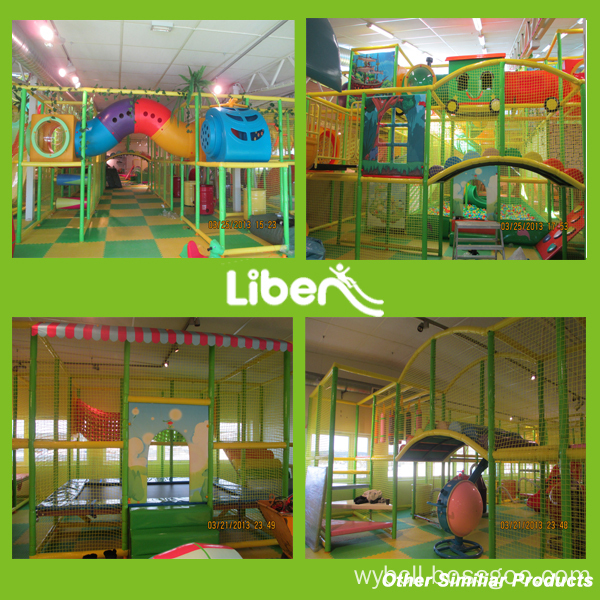
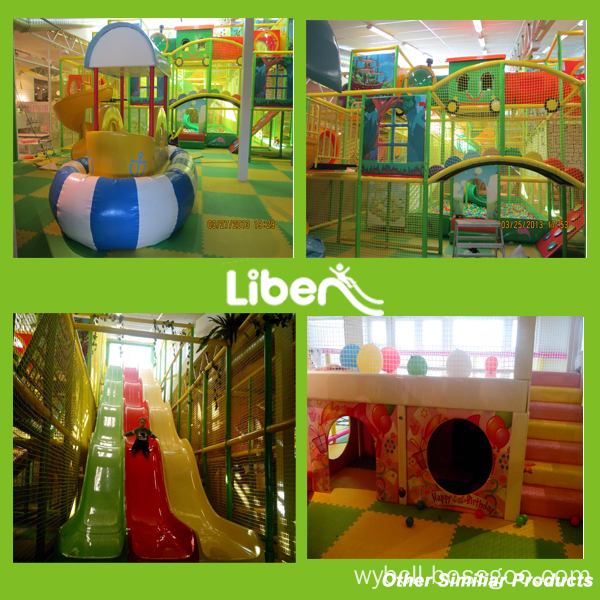
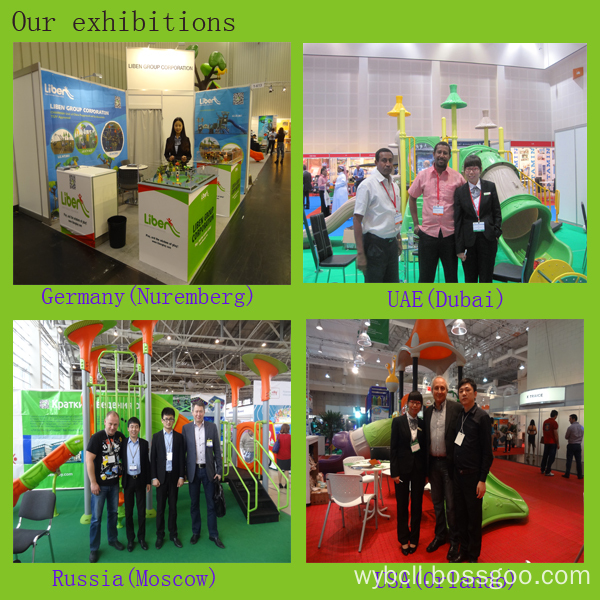
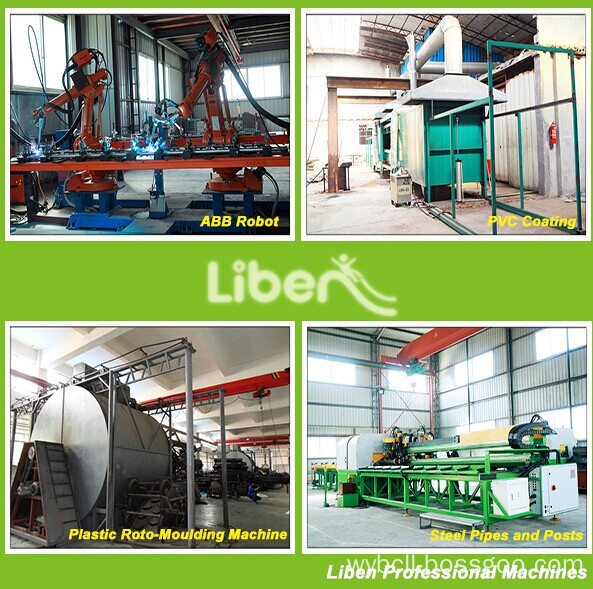
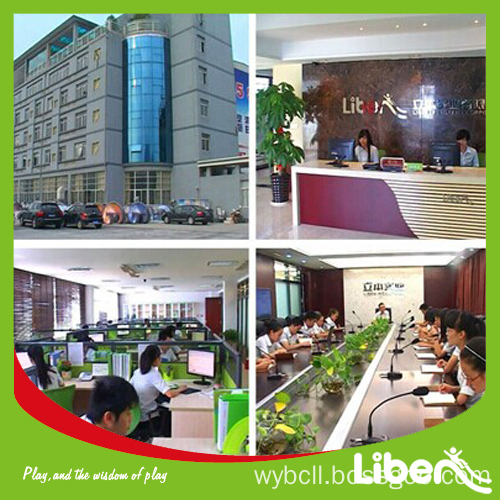
Kids Plastic Playhouse, Plastic Outdoor Playhouse, Cheap Plastic Playhouse, Childrens Plastic Playhouse
Liben Group Corporation , http://www.indoortrampoline.de