Dirty plates are divided into full-size large areas from dirty and local dirt, the reasons are many. The improper adjustment of the pressure of the water roller and the printing plate, the inappropriate ratio of the water roller and the ink, the proportion of the wetting liquid, the improper spread of the printing plate pad, and the quality problem of the printing body can easily make both sides of the printing plate dirty. During the printing process, sometimes there are defects on both sides of the offset printing plate. The reasons for the dirt on both sides of the plate are analyzed below.
Water roller uneven
When adjusting the contact pressure of the water supply roller to the hydrophobic roller, be sure to pay attention to the symmetry of the direction of the eccentric bearing, otherwise it will cause the water roller to be not parallel to the plate cylinder and the hydrophobic roller, and the flannel of the water roller will be easily axial. Pushed into a spiral shape, the water can not be even. If the eccentricity of the water roller is adjusted at both ends, the pressure of the water roller will be uneven, and the side of the printing plate will be easy to get dirty. Therefore, when measuring the pressure of the water roller, several points can be measured. It is necessary to measure both ends and measure the middle.
In addition to accurately adjusting the contact pressure of the water roller, it is also very important for the daily proper maintenance of the water roller.
1. In normal offset printing operation, the water roller should be kept clean and free of oil.
2. Water roller sleeves should always be moist and have a certain amount of moisture.
3. Clean the water roller regularly. If the water roller can be washed, it will be washed with too much oil, and when it cannot be cleaned, it is necessary to replace the new water jacket in time to prevent the plate from becoming dirty. Another method can effectively prevent the water roller from sticking ink. That is, when printing, a small amount of hydrophilic colloidal substance, gum arabic, is added to the water bucket solution, which can effectively increase the hydrophilicity of the water roller, and use the sponge and other hydrophilic materials. The material wipes off the emulsified oil stains in the hopper solution and absorbs the ink on the surface of the water roller.
The middle of the water roller is fine
When the water roller is processed on the lathe, it is an elastic body, and the two ends are subjected to a large force, the middle one is vibrating, and the pressure is small. Most of them have different degrees of shape error of two thin intermediate ends, and gaps exist at both ends. Easy to get dirty. In addition, the two ends of the water roller sleeve are thinned and thinned when being sewed, and the moisture absorption of the two heads is small, so that the surface of the printing plate cannot be sufficiently wetted, and both sides are likely to be dirty.
Remedy: Cut the size of the water velvet sleeve to be consistent with the water roller, not too short. When the sewing thread is sewn evenly, do not over-tighten it. Make sure that there is no room for closing and avoid making the two ends of the roller sleeve too thin.
Plate liner size is too small
Under normal circumstances, the lower edge of the printing plate should be filled with liner paper. In order to prevent the two sides of the printing pad from soaking into the water, the lateral size of the liner is smaller than the size of the printing plate. However, if the size of the liner paper is too small, the pressure on both sides of the printing plate will be insufficient, resulting in poor contact between the printing plate and the water roller and dirtiness.
Remedy: When cutting the offset liner, the lateral dimension is controlled within 10 to 20 mm smaller than the printing plate. To prevent damage to the liner due to water ingress, a layer of Fan Ting Lin may be applied on both sides of the liner or Butter, oil, and the use of oil and water repel the truth, to avoid wet liner paper, improve the use of results. If the cylinder liner paper is wetted, the drum casing is easily rusted.
Two ink sticks on the water roller reduce the water transfer performance
If there is too little water control on both sides of the plate layout, it will result in ink sticking on both sides of the water roller due to insufficient water supply, causing dirt on both sides of the plate.
(author Wang Xincheng)
Water roller uneven
When adjusting the contact pressure of the water supply roller to the hydrophobic roller, be sure to pay attention to the symmetry of the direction of the eccentric bearing, otherwise it will cause the water roller to be not parallel to the plate cylinder and the hydrophobic roller, and the flannel of the water roller will be easily axial. Pushed into a spiral shape, the water can not be even. If the eccentricity of the water roller is adjusted at both ends, the pressure of the water roller will be uneven, and the side of the printing plate will be easy to get dirty. Therefore, when measuring the pressure of the water roller, several points can be measured. It is necessary to measure both ends and measure the middle.
In addition to accurately adjusting the contact pressure of the water roller, it is also very important for the daily proper maintenance of the water roller.
1. In normal offset printing operation, the water roller should be kept clean and free of oil.
2. Water roller sleeves should always be moist and have a certain amount of moisture.
3. Clean the water roller regularly. If the water roller can be washed, it will be washed with too much oil, and when it cannot be cleaned, it is necessary to replace the new water jacket in time to prevent the plate from becoming dirty. Another method can effectively prevent the water roller from sticking ink. That is, when printing, a small amount of hydrophilic colloidal substance, gum arabic, is added to the water bucket solution, which can effectively increase the hydrophilicity of the water roller, and use the sponge and other hydrophilic materials. The material wipes off the emulsified oil stains in the hopper solution and absorbs the ink on the surface of the water roller.
The middle of the water roller is fine
When the water roller is processed on the lathe, it is an elastic body, and the two ends are subjected to a large force, the middle one is vibrating, and the pressure is small. Most of them have different degrees of shape error of two thin intermediate ends, and gaps exist at both ends. Easy to get dirty. In addition, the two ends of the water roller sleeve are thinned and thinned when being sewed, and the moisture absorption of the two heads is small, so that the surface of the printing plate cannot be sufficiently wetted, and both sides are likely to be dirty.
Remedy: Cut the size of the water velvet sleeve to be consistent with the water roller, not too short. When the sewing thread is sewn evenly, do not over-tighten it. Make sure that there is no room for closing and avoid making the two ends of the roller sleeve too thin.
Plate liner size is too small
Under normal circumstances, the lower edge of the printing plate should be filled with liner paper. In order to prevent the two sides of the printing pad from soaking into the water, the lateral size of the liner is smaller than the size of the printing plate. However, if the size of the liner paper is too small, the pressure on both sides of the printing plate will be insufficient, resulting in poor contact between the printing plate and the water roller and dirtiness.
Remedy: When cutting the offset liner, the lateral dimension is controlled within 10 to 20 mm smaller than the printing plate. To prevent damage to the liner due to water ingress, a layer of Fan Ting Lin may be applied on both sides of the liner or Butter, oil, and the use of oil and water repel the truth, to avoid wet liner paper, improve the use of results. If the cylinder liner paper is wetted, the drum casing is easily rusted.
Two ink sticks on the water roller reduce the water transfer performance
If there is too little water control on both sides of the plate layout, it will result in ink sticking on both sides of the water roller due to insufficient water supply, causing dirt on both sides of the plate.
(author Wang Xincheng)
Mostly sizes we make for Baby Shoes are in 0-6month, 6-12month, 12-18month, 18-24month, and we also use hard rubber sole for kids moccasins in larger sizes beyond 2 years old,
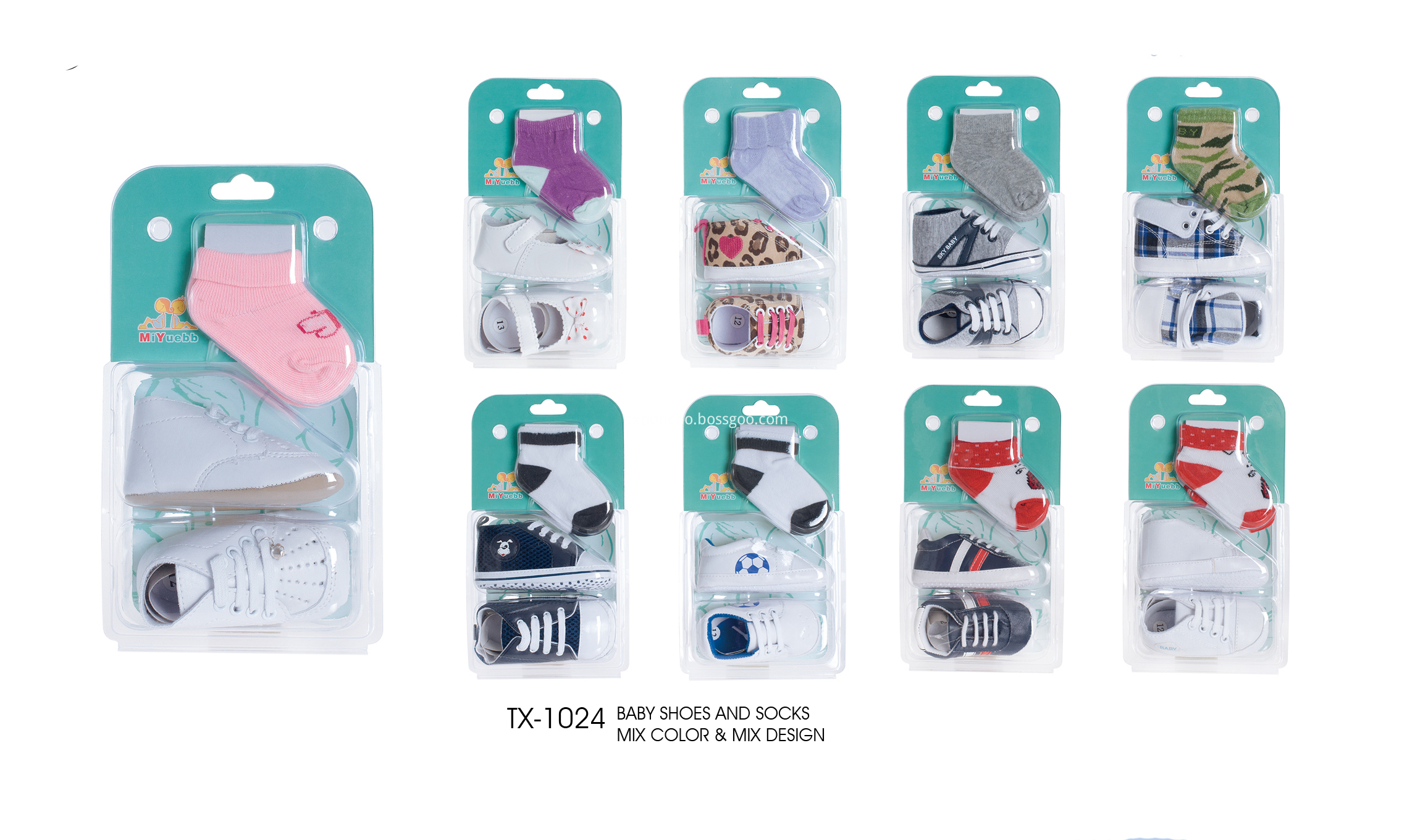
We are a Professional Baby Ribbon Shoes manufacturer is located in China, including Baby Walking Shoes, Baby Socks ,Baby Cotton Shoes,Baby Moccasins, Soft Shoes etc.
Baby Shoes
Baby Ribbon Shoes,Baby Walking Shoes,Baby Cotton Shoes,Baby Moccasins, Soft Shoes
Zhaoxian Tengxing Plastic Fashion Co., Ltd , http://www.goodraincoat.com